Equipment for the manufacture of balusters. Production of concrete balusters for fencing. Baluster manufacturing technologies
Balusters are vertical support posts, the main elements of the railing. Whether it's a railing for a staircase, a bridge balustrade or a veranda railing, it doesn't matter, the device and purpose are the same everywhere. From this article you will learn what balusters are and how to make them yourself.
What is a balustrade? - this is a railing of figured columns connected from above by a horizontal beam, a handrail;
Fencing posts perform several functions:
- railing support;
- security;
- decorative element.
They can be visually divided into three parts:
- handrail support;
- central part;
- baluster base.
The base of the baluster or pint is that part of the post that is attached to the steps or balusters. The central part performs protective and decorative functions. A handrail is installed at the upper end. This part of the post is always made with a small allowance so that you can adjust the height of the railing.
For the manufacture of a classic balustrade, both traditional materials are used: wood, metal or concrete, as well as modern analogues: glass, plastic (PVC), polyurethane.
If you know what balusters are and have seen them more than once, then you will agree that the most popular material for their manufacture is still wood. This is due to the ease of processing the material and the possibility of giving any shape.
Wooden balusters for stairs
Wooden balusters are made using three main technologies:
Stair railings consist of balusters (racks) and pillars. Entrance poles are mounted at the beginning and end of flights of stairs, as well as at the corners of the landings. They are made in the same style and differ only in height and cross section, for example, if square balusters have a side of 45 to 50 mm, then fence posts - from 80 to 100 mm. The height differs by 10-20 cm.
In accordance with GOST 25772-83, it must be taken into account that in order to ensure the safety of the operation of the stairs, the distance between the balusters must be:
- stairs for the house - no more than 15 centimeters.
- combined or screen railing - 30 cm.
- stairs in children's institutions - 10 cm.
Flat wooden balusters
As a rule, racks in cross section have the shape of a circle or square. However, along with models of the traditional form, flat balusters are also used, which are used not only as a fence for flights of stairs, but also for gazebos, verandas, balconies and other structures.
Flat carved balusters can be installed close to each other, forming a single pattern. Thus, it is possible to perform complex ornaments large sizes, thanks to which wooden balustrades acquire a finished appearance.
To make flat wooden balusters, you need to stock up on blanks right size. Choose a suitable pattern and sketch. Then transfer the drawing to the workpiece and cut it out with a jigsaw along the contour.
When the ornament is sawn out, they proceed to finishing with cutters - all patterns and decorative elements are turned, made smooth and symmetrical.
What type of wood to choose?
It is very important to choose the right material, because not only the cost of the product, but also its performance characteristics. It is recommended that the steps and pillars for stairs be made of the same wood. This will avoid deformation of the structure in the future. For the production of wooden racks, hardwoods are used.
Oak
Balusters made of oak are characterized by high wear resistance and strength, resistance to decay. The wood is dark brown or light brown in color. An important advantage is that oak balusters are not subject to cracking and do not warp. The dense structure allows you to perform the most small parts and even curved elements - all kinds of balusters and material processing methods are available.
Beech
Balusters made of beech are almost as hard as oak in quality and hardness, while they are easily processed and bent. Wood lends itself well to impregnation various formulations, which contributes long term services of varnish and colorful coatings.
The disadvantage of this type of wood is that when it dries, it warps and rots a lot, so it is recommended to use beech balusters only in rooms with low humidity. Beech is used to imitate such valuable breeds like walnut or mahogany.
Ash
Outwardly, ash wood resembles oak, but is inferior to it in hardness and strength. The structure is elastic, dense and heavy. His hallmark is durability and resistance to decay. Ash has a beautiful texture of yellowish color with dark and light stripes. Balusters made of ash can withstand significant loads, especially bending loads. The wood warps a little and bends well when steamed.
Birch
This tree is used somewhat less frequently than the species described above. Birch has average density, hardness and strength with good toughness. The disadvantage of birch is its tendency to crack, significant shrinkage, susceptibility to decay. But at the same time, birch is easy to process, easy to glue, polish, paint. Birch, when using appropriate dyes, is easily given the appearance of precious woods: gray maple, mahogany or walnut.
Pine balusters
Pine belongs to soft breeds, due to which it is easily processed by cutting tools and lends itself well to grinding. Pine balusters are immune to temperature changes and are resistant to fungal attack. The color of the wood varies from light yellow to yellowish red. Pine has areas with different porosity, so the paint is absorbed unevenly, which reduces the quality of the coating.
Larch
Balusters made of larch have a red-brown or brown color. This tree is inferior to oak in hardness, but surpasses it in strength, and, over time, wood, due to the special composition of the resin, only becomes stronger. Larch is not subject to warping, but during the drying process, internal cracks may occur. Railings and balusters made of larch are durable and do not rot.
Racks can be made from rarer and expensive varieties trees that you can't buy in the store. In this case, you should contact the manufacturer directly or a specialized company that produces custom-made balusters.
Baluster making machine
Manual frezer
Milled balusters can be cut into homemade machine which is shown in the photo. This requires a cylindrical workpiece.
A platform is movably mounted on a threaded shaft (1) (2 - in the figure it is in a raised state), on which, in turn, an electric drive (3) with a wood cutter (4) is fixed.
When exposed to the handle (5), the wooden blank (6) starts to rotate. At the same time, the platform moves along the shaft in a horizontal plane. As a result, a spiral line is cut on the workpiece. The depth and width of the notch is determined by the size of the cutter, and the pitch of the helix is determined by the size of the gear. Depending on the complexity of the task, the manufacture of balusters manual router takes from 15 minutes to several hours.
The production of wooden balusters can be simplified by using a machine with a copier. In this case, a template is first prepared, as shown in the photo.
The essence of this method is that the depth of the cut is not adjusted manually, but with the help of a thrust-guiding roller that moves along the template. First with a roller larger diameter roughing is carried out. Then a roller of a smaller diameter is put on and performed final finishing. The machine for the production of balusters is shown in the figure.
A manual milling machine is mounted on a movable carriage. The cutter can move along a line perpendicular to the axis of rotation. The distance to the center of the workpiece depends on the position of the guide roller moving along the template.
When using this method, balusters and railings in general are obtained in a more complex and perfect form. CNC machines allow you to make the most beautiful specimens of any level of complexity.
Manufacturing of wooden balusters
The manufacture of wooden balusters is a complex process that requires certain skill and equipment that will ensure the rotation of the workpiece along the longitudinal axis. The most commonly used for this purpose lathe.
The production of balusters consists of several stages.
Design
First of all, it is necessary to take into account the size of the stairs - the number of racks that need to be made will depend on this. The height of the baluster is defined as the difference between the total height of the railing and the thickness of the handrail with the step covering. As a rule, the value ranges from 65 to 100 cm.
Next, you need to decide on the design. Samples of balusters can be found on the Internet. After the sketch is selected, it is necessary to transfer it to the drawing, indicating the dimensions. In this case, all sections are numbered and the depth of the cuts is noted. For example, a drawing of a baluster of the simplest form might look like this:
All marks must be transferred to the workpiece and numbered in order to know which tool to use for a particular part.
Baluster turning
It is very important to fix the workpiece strictly in the center in order to avoid beats and distortions. If the workpiece has the shape of a square bar, then diagonals are drawn at the ends, and the baluster is fastened strictly at the point of their intersection. In this place it is necessary to make a recess.
In order for the turned balusters to have a rounded shape, sharpening is done with the help of a reyer. To simplify the process, professionals recommend first grinding off the corners, turning it into an octahedron. To do this, a cutter of the required width, located perpendicular to the axis of rotation, makes a straight cut to the required depth, and the workpiece takes on the following form:
Fastening wooden balusters to the stairs - video and photo instruction
Balusters made of wood can be installed on the steps of the stairs, or on a bowstring or kosour. For fixing, hardware, anchors (dowels) or special brackets are used. In this case, several rules must be observed:
- the distance between the balusters should be no more than 150 mm;
- height from 90 cm to a meter;
- entry posts are installed at the beginning and end of the flight of stairs and at the corners of the site.
It should be remembered that fastening balusters with nails does not provide sufficient strength to the structure. And later causes squeaks and discrepancies in details.
Before you install the pillars on the stairs, you need to make holes in the ends, strictly in the center. To do this, you can make a simple device, consisting of a drill mounted on a chipboard shield, and a wooden block with a centering hole. To prevent the rack from staggering, a bar is used to fix its position.
This device allows you to drill even recesses in the base of the balusters, the diameter of which is 2 mm smaller than the diameter of the fastener.
The installation of balusters made of hard wood is carried out using metal studs with a cross section of 6-10 mm and a length of 60-100 mm or wooden dowels with a diameter of 8 to 14 mm and a length of 50-80 mm. Stair poles are fixed with larger fasteners.
In the example, we will use 8x100mm metal studs for the uprights and 10x100mm for the posts.
When the installation of the balusters is completed, you can attach the handrail. To do this, we cut off the upper part of the two extreme racks at the right angle, apply a rail to them and mark the place for the cut on the rest. In accordance with the markup, we saw off all the tops.
When working with a miter saw, wrap the cut with tape, so you can avoid chipping the wood.
With self-tapping screws we fasten the railing rail to the uprights, on which the handrail is subsequently mounted.
The ends of the handrail are cut so that they stand close to the posts. Niches for fasteners are cut out on the reverse side.
At the end, we fix the handrail to the railing rail with self-tapping screws and close it with a decorative overlay, cut into pieces and glued between the posts.
Metal balusters for stairs
Compared to wood, metal balusters have a number of advantages, the main of which are their durability, ease of maintenance, and the ability to use both indoors and outdoors. In addition, they look aesthetically pleasing and blend perfectly with other materials. For example, you can see combined balusters, the base of which is made of of stainless steel, and the core is made of glass or wood.
Metal railings, due to the variety of forms, can become an adornment of any architectural ensemble. They are used not only as a fence for flights of stairs, but also for balconies, terraces, etc. Forged balusters for stairs look especially advantageous. Let's see what kind of metals are used:
Stainless steel
Stainless steel balusters are undoubtedly the most sought after. Benefits include:
- ease of manufacture of racks. Modern methods metalworking allows you to make both seamless railings, made using welding, and modular, for the assembly of which hardware and brackets are used;
- high anti-corrosion performance. Chrome-plated stainless steel balusters are excellent for use in environments with variable temperatures and high humidity. Such products successfully resist corrosion caused by acids, chlorine solutions, alkalis and other aggressive substances;
- strength steel allows you to significantly reduce the thickness of the racks and give the whole structure a lightness and a feeling of airiness. The material does not lose its properties when low temperatures, which allows the wide use of stainless steel balusters for outdoor stairs.
Cast iron
Cast iron balusters are reliable and elegant railings for stairs. This material has its advantages:
- durability. Cast iron does not lose its aesthetic and physical properties over a long period of time, remaining beautiful and durable. It can be said without exaggeration that the staircase with cast-iron balusters is built to last;
- mode of production cast iron railings (casting) allows you to make a product with the most complex configuration - any shape and content is available.
- functionality. Cast iron balusters are suitable for stairs made of any material, be it wood, metal or reinforced concrete. Based on this, certain methods of fastening to the steps are used:
- using welding or brackets for metal stairs;
- concreting in steps for monolithic structures;
- threaded connections or installation on a dowel for solid steps.
iron balusters
Iron lends itself perfectly to forging, which makes it possible to make beautiful railings. Often, forged balusters are made to order, which allows you to adjust the balustrade to the existing design of the room, porch or balcony. Iron is susceptible to corrosion, but the use of modern protective coatings provides resistance to environmental influences.
Forged balusters have only two drawbacks: high price and manufacturing complexity.
Metal processing methods
Metal balusters are made by casting or forging.
Forged balusters
For wrought iron railings, the most suitable are soft grades of iron, steel or copper. There are two processing methods:
- cold forging;
- hot.
In the first case, a workpiece is cut out of metal, which is subjected to stamping or bending on special equipment. Further, various forging elements and decorative inserts in balusters are welded to it. Method cold forging allows you to independently make simple elements of fences. The advantage of this method is its low cost, and the disadvantage is the high labor intensity of the process.
During hot forging, the workpiece is heated to a high temperature, at which the metal becomes ductile and easily acquires desired shape. In this case, it is possible to manufacture a more perfect form of a balustrade, but this method requires deep knowledge and considerable experience in working with metal.
Cast balusters
The metal is heated to higher temperatures than forging, at which it is melted and liquid is poured into the mold. Most often, cast balusters are made of steel or cast iron. There are several types of casting:
- in sandy-clay forms;
- investment models;
- in a chill mold;
- vacuum casting and others.
The main advantage of this method is its wastelessness and the ability to make any version of the baluster itself. perfect shape, exactly repeating the workpiece.
How to DIY
To make metal racks in " home environment» the cold forging method is used. For convenience, you can use a homemade bending machine, for example, as in the photo.
Depending on the shape of the circle, any shape can be given to the metal profile - made different types balusters. If the product consists of several elements, then they are connected by spot welding.
Do-it-yourself baluster installation
When installing metal racks, two main methods are used:
- installation on a step- the most popular method in which anchoring of balusters is used;
- at the end of the step. A more complex option, when the railing is mounted on special brackets and does not reduce the usable width of the steps;
Concrete balusters
Concrete balustrades are functional and aesthetic, they will give your home an aristocracy and elegance. Due to the qualities of the material, the product is not afraid of dampness or sudden changes in temperature. It is strong and durable.
Concrete balusters are made by pouring mortar into a mold. To make a mold, you need a model, which can be a ready-made stand made of concrete or a blank made of any other material. Such a model can be made from plaster on a simple machine (shown in the figure).
1 - handle for rotating the workpiece;
2 - baluster template;
3 - the axis on which the gypsum mixture is applied;
4 - axle mount.
The principle of operation of the machine is as follows: a gypsum mortar is fed to the rotating axis, the excess of which is cut off by the edges of the template and flows into the tray. Gypsum gradually accumulates, forming a baluster of the desired shape. After the solution hardens, the disc is scrolled several more times, cutting off upper layer. This is necessary because the gypsum expands when dried, respectively, and the size of the product increases.
The rod is pre-wrapped with paper so that the gypsum balusters do not stick and can be easily separated.
The resulting workpiece must be processed so that there are no open pores left. To do this, the surface is puttied and cleaned with sandpaper. After that, it must be primed and varnished. A model prepared in this way lasts much longer.
From the made blank, you can remove plaster, glue or cement lumpy forms.
Such a machine can be used not only for preparing models necessary for the manufacture of molds, but also directly for the production of concrete racks. How this is done is shown in the video.
First, a disk is cast, the diameter of which is approximately 5 centimeters larger than the section of the plaster model, and glued to its end, serving as a base. Further, places are marked on the disk for fractional pieces, from which the shell of the form for balusters will be formed. In these places, holes are drilled on the reverse side - these will be locks with which it will be possible to assemble the form without distortions.
The whole structure is divided in half, into two rows. Next, methodically collect the first row, as shown in the figure. All parts are lubricated with a release agent. Gypsum mortar is poured between the model and the formed bead.
Baluster molds are cast from plaster, to which lime is added so that the material does not deform, and lemon acid so that it does not catch on so quickly.
After solidification, the structure is disassembled and the edges are cut. Holes are drilled on the upper part for pieces of the second row. Details are varnished and lubricated. The structure is assembled again, a side for the second sector is built, everything is smeared and filled with a gypsum solution.
Finished sectors are interconnected. For greater strength, you can still cast the outer casing in the same way as the mold itself was cast, only it is made of two halves. For ease of use, handles are inserted into it during casting. The form is ready, now you can start making the pillars.
Now in stores there are many molds made of polymers, fiberglass or other materials. Plastic molds are easy to use and durable. With their help, you can make balusters of any configuration with your own hands.
Production of concrete balusters
Our mold can be used for both casting and beating balusters. Both methods are widely used and have their own advantages.
Beating balusters
The peculiarity of the process is that the balusters are beaten using an almost dry solution. To do this, the sand is mixed with cement and aggregate in a dry form. Then they are evenly poured with small portions of water and thoroughly mixed.
You can understand that the solution is ready and meets the requirements as follows. Take a small amount of the mixture and squeeze it in your hand. If, after unclenching the hand, the substance has not disintegrated, it is ready for use.
The prepared solution is poured into the mold in small portions, in layers from 50 to 100 mm thick, and compacted well, as shown in the video. Thus, the form is filled to the very top.
Next, carefully remove the casing and pieces of the form. Be extremely careful, because the broken balusters have not yet had time to finally grab. Before complete drying, the product should not be subjected to any mechanical stress. And only in two days the rack will be ready for installation.
Rack casting
For casting concrete balusters, a mold with an upper piece in the form of a lid is used. Gypsum or concrete mortar, the neck is tightly closed, and by rotating the mold in a horizontal plane, a more uniform distribution of the solution over the vessel is achieved. After a couple of hours, the mold is disassembled and the casting is removed. By repeating the procedure, you can make the required number of racks with your own hands.
Balusters and poles made by the described methods do not require additional grinding and puttying.
Installation of concrete balusters - installation of a concrete balustrade
It is necessary to think in advance about how you will fix the balusters. To do this, metal inserts are installed in the upper and lower parts of the mold - pins 10 cm long for the bottom and 5 cm for the top. Sometimes thin reinforcement is used, passing through the entire rack.
If a concrete balustrade will be installed on metal staircase, then this bookmark is simply welded to flight of stairs. If the staircase is concrete, then it is necessary to drill holes for the anchor in the steps and, after installing the racks, fill them with mortar. The video perfectly shows how to properly install balusters and poles - make a balustrade.
Stone balusters - stone balustrades
Balusters from natural stone at the same time they are both the most beautiful and expensive. Railings from massive pillars create special charm majesty and monumentality. A stone balustrade will serve as a wonderful interior decoration, emphasizing the luxury of home furnishings and personal plot. For the production of stone balusters, the following rocks are used:
All of the above rocks are natural, and therefore expensive. What to do if you don't have enough money to buy natural stone. There is an exit. Today, when technology has gone very far, balusters made of artificial stone have become widespread. Look at the photo below. If you think that these wonderful railings are made of natural rock, rare and very expensive. You are wrong. This stone balustrade is the result of innovative technology.
Often, non-natural material looks much better. Modern technologies are capable of many things, including imitating naturalness. The palette of colors and shades, patterns and textures will be much wider for stone balusters made in the laboratory.
This product has serious advantages over natural material:
- a wide choice of colors and textures;
- imitation of absolutely any natural stone;
- excellent performance characteristics;
- affordable price.
Artificial stone railings are resistant to aggressive substances, such as household chemicals. Therefore, in the house, such products are preferable to natural ones.
Production process
Artificial stone balusters are produced by casting, similar to concrete ones. First, a wooden blank is turned. According to it, a plaster mold is made, consisting of several parts. Inside, the surface is coated with a layer of water-repellent lubricant. This is followed by a key manufacturing step: a special solution is poured into the mold, which, after drying, will become artificial stone. The mold is placed on the centrifuge and quickly rotated in a horizontal plane to distribute the mixture evenly. After the solution hardens, the form is disassembled. And the finished column is subjected to finishing to obtain a shine.
Glass balusters
Now, more and more often, various elements of stairs, including railings, are made of traditional materials, for example, from glass. Such pillars in combination with glass steps will give a special look to the stairs, creating a feeling of lightness. Glass harmonizes with all kinds of materials, from metals to plastics, which makes it possible to create combined balusters.
For production use multilayer silicate glass, the individual layers of which are glued together by a strong polymer film. Such glass is also called building triplex. It is almost impossible to break it: the material will not withstand a strong blow, but it will not disintegrate into small fragments - cracks will only appear on it.
Glass balusters and poles are fixed with wood or metal fasteners. It can be hinges or special nozzles. Flat screens made of glass are inserted into a pre-cut groove or mounted on brackets.
Racks made of other materials
Polyurethane balusters
Inside the polyurethane sheath is metal pipe, which gives rigidity and strength to the entire structure. Polyurethane balusters are able to withstand loads no less than traditional materials. But the damaged part can be easily dismantled and replaced with a new one. Among their advantages is also ease of manufacture, speed of installation and low cost.
plastic railing
They are made of polymer plastics, which are devoid of all the shortcomings of natural materials and can imitate almost any of them, for example, wood. As a rule, high-impact polystyrene or PVC is used, the structures of which are lightweight and high strength.
Plaster balusters
Often used as templates and samples for the manufacture of racks from other materials. By appearance very similar to concrete counterparts and are also produced. The main advantages are:
- the possibility of implementing the most daring design decisions;
- ecological purity of raw materials;
- resistance to shrinkage and deformation;
- light weight and ease of installation.
At the same time, gypsum balusters are durable, and if necessary, such a structure can be easily repaired.
There are other types of balusters from various materials and designs.
Conclusion
Now you know what a baluster is and what a balustrade is and are able to use the information received when buying or manufacturing these staircase elements. Do not be afraid to experiment and the result will exceed all your expectations.
With my own hands, one of milestones is the manufacture of fences. They are very important, as they provide a safe ascent and descent and give the march a finished, harmonious look. The price for the manufacture and installation of railings for stair structures is quite high. However, safety and aesthetics should not be neglected. You can make and install balusters with your own hands. With the right material and the observance of all technologies, you can get a result that will please you.
The choice of material for balusters
Balusters are special holding posts that are installed between the canvas of the steps and the handrails. For the manufacture of such supports, you can use a variety of materials. But, the most popular are carved balusters made of wood.
Visually, the racks can be divided into three parts:
- Base supports or pints are attached to the balustrades or steps.
- central part racks perform protective functions.
- support for handrail. This part of the baluster must be made with an allowance so that it remains possible to adjust the height of the railing.
For the manufacture of supports, it is very important to choose the material. This will depend on the performance of the products.
What kind of wood to choose
To avoid future deformation of the structure - steps, railings and racks for stairs are recommended to be made from the same wood. Select hardwoods.
Larch.
From this tree, durable products of brown or reddish-brown color are obtained. Thanks to the special composition of the larch resin, the balusters and railings made of larch will only become stronger over time. The tree is not subject to rotting, however, cracks may occur during its drying.
Pine.
The color of pine balusters can be from light yellow to yellowish red. Pine lends itself well to grinding and is easily processed cutting tool. Products from it are not affected by the fungus and are able to withstand temperature extremes.
Birch.
Birch products can be easily painted and give them the look of valuable tree species. Birch has good toughness, but average hardness and density. It can be easily processed, polished and glued. However, wood is susceptible to decay and may crack when dried. That is why it is rarely used for the manufacture of railings and balusters.
Ash.
The tree has a beautiful structure, when steaming it bends well and warps a little. Products from it are yellowish in color with light or dark stripes. The structure of the wood is dense, elastic and heavy. Supports and railings made of ash will last a long time and will be able to withstand significant loads.
The tree is used to imitate valuable species. Products from a beech well bend and are processed. To extend the life of paint and varnish coatings, balusters and railings can be impregnated with various compositions. However, beech products should only be installed in rooms with low humidity, as the wood is prone to rotting.
Oak products have a light brown or dark brown color. They are characterized by strength, wear resistance and resistance to decay. Oak railings and balusters will not warp or crack. The dense wood structure can be used to produce curved elements and very small parts.
Supports can also be made from more expensive and rare tree species. If you can’t buy them in the store, you will need to contact the manufacturer directly and place an order.
Types of balusters. Photo examples
There are three types of wood racks that are hand carved or lathe:
- flat supports can be made with a through figured thread (pictured) or simply with a contour shape.
- Faceted threaded racks are made by hand.
- Balusters round section can be done both manually and on the machine.
Flat balusters
If flat posts will be made to protect the porch from dirt, dust and wind, then when making them, a shallow thread should be used, and they should be installed close to each other. With the help of a shallow carving, you can create a border of a pattern without leaving through openings.
If a protective wall is not needed, then a thin openwork carving, which looks like a lace pattern, can be used to decorate the product.
Types of flat railings:
- Racks can be made absolutely similar. In this case, they are installed in any order (pictured).
- The decorative effect of balusters without internal curly carving is achieved due to the contour shape of the products.
- The third type of support is when the pattern of the next baluster is a continuation of the pattern of the previous one. In this case, they should be installed carefully so as not to confuse the order.
Round balusters
Quite popular supports in the form of round columns. They are made by hand or on a machine. The columns can be with a variety of carved patterns and have a different cross section.
It is quite simple to make such products on a lathe. Handwork requires skill and skill.
To fence the balcony, the posts in the cross section must be wide enough.
Making balusters with your own hands
For the manufacture of wooden supports requires equipment and a certain skill. Most often, a lathe is used for this.
Making round balusters
Before starting work, you should design the shape of the products. This is necessary in order to know where it will be necessary to change the support roller in the machine and which chisel to use.
Sequence of work:
- The workpiece is fixed on the machine (pictured). Sometimes a hole is made in its ends for this.
- If the workpiece is square, then its corners are ground with the help of a semicircular chisel.
- With the help of a reyer at an inclination of forty-five degrees, fine turning is performed.
- Figured elements are machined on the machine, with a chisel or manually according to the template.
The finished column is polished and varnished.
Wooden railing installation
In order for the ladder structure to turn out to be reliable, some rules must be observed during its construction:
- the height of the railing must be at least 90 cm;
- recommended support step width - 15 cm;
- railings should be comfortable and well crafted;
- balusters must be fixed in two places.
Installation process consists of several stages:
- First of all, extreme supports are installed.
- Using a level or twine, the locations of the racks are marked.
- The middle of the balusters is marked with a construction marker.
- The upper part of the supports is sawn off at the same slope under which the entire staircase structure is located.
If the pillars are also attached on top of the bowstring, then it will also be necessary to adjust the lower sections.
Types of fastening balusters
There are three types of fastening balusters:
- self-tapping screws;
- dowels;
- hairpins.
Installation with studs.
In the middle of the support, a hole is made with a depth of 80 mm and a diameter of 12 mm. The zinc-plated stud is inserted into the hole and fixed with glue. The studs should protrude from the holes by 50 mm (pictured).
In the steps, according to the markings, holes are made into which the supports on the studs are inserted. Everything is fixed with glue.
Installation with self-tapping screws.
This is the most easy option rack mounts. The main thing is to make sure that the screws are made of stainless steel.
The column is installed vertically and a self-tapping screw is screwed into it from the side at an angle. The part of the self-tapping screw that came out of the support should be screwed into the step.
Installation on dowels.
Holes are prepared in the steps and on the sections of the supports with a drill, in which dowels smeared with glue are attached. The holes of the racks are treated with glue and the balusters are installed on the dowels. A level or plumb line checks the verticality of the support.
After the glue dries, you can attach the handrails.
Do-it-yourself railing installation
Handrails are mounted in several stages:
- The upper part of the extreme supports is cut off at the desired angle.
- With the help of a rail, the cut points of the remaining supports are marked.
- The tops of all balusters are cut off.
- The rail, on which the railing will subsequently be installed, is attached to the racks with self-tapping screws.
- The ends of the railing are cut along the last columns.
- Holes for fasteners are cut out on the reverse side of the handrails.
- The railing is fastened to the rail with self-tapping screws and covered with a decorative overlay.
Fencing for ladder construction installed. Now climbing and descending the stairs is safe, and the design itself looks harmonious and beautiful. The value in making balusters with your own hands is that you can make parts of the right size with what you see in the photo and the pattern you like.
Making balusters will not be difficult for you if you have woodworking skills. Balusters are vertical supports that are important elements stairs. They perform a number of functions:
- balusters are needed in order to support the handrail;
- they are designed to ensure the safety of people climbing stairs.
Balusters are an important part of the decor of the room. They are made up of several structural elements. The basis - a rack which is established on a step. Speaking about the central part of the uprights, keep in mind that their functions are exclusively protective and decorative.
Baluster manufacturing technologies
To produce wood racks, you need a machine. Can be called following technologies production:
- The most common type is the production of turned products.
- Milling. In this case, cutting is done on the racks. decorative elements decorate the product.
- Wooden balusters with carvings. Today, the thread is applied not by hand, but by processing the workpiece on high-precision machines.
If you look at the cross section, you can distinguish the following forms:
- square;
- round.
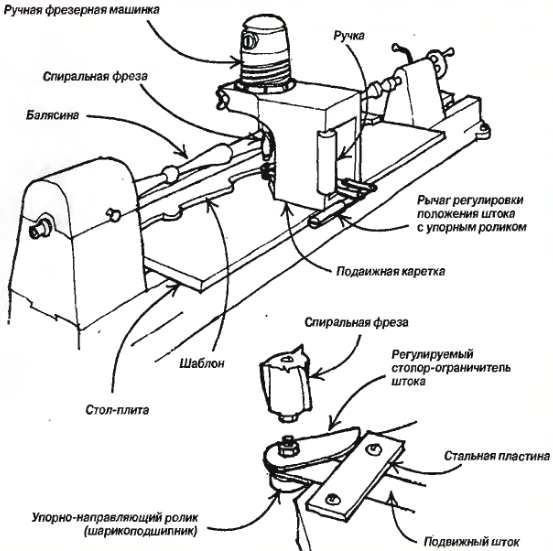
In addition, flat racks are often made, which are widely used in public buildings and private homes. Flat balusters are installed tightly to each other. This approach allows you to create quite complex ornaments, large in area.
The production of flat wooden balusters does not require much time. The process begins with the preparation of blanks of the required size. In addition, you need to select a pattern, and then create a sketch based on it. After that, take a sample, apply a contour to the workpiece. Next, you must take a jigsaw and cut out the workpiece. Then start finishing, cut all the elements of the balusters with cutters.
Work so that all parts become symmetrical. When the process is completed, glue the elements, install the structure. Coat the balusters with varnish.
How to choose lumber for the production of balusters
The final cost and performance characteristics of the product depend on the choice of lumber. Masters advise making balusters and steps from one type of wood, this helps prevent the structure from deforming in the future.
For the production of columns, it is better to choose lumber from the following types of wood:
- nut;
- ash;
- larch,
- Pine.
For the production of wooden balusters, it is better to buy hardwood lumber. For example, oak is very well suited, it is resistant to wear. Oak is not very susceptible to decay, it will serve for a long time. Twisted columns are made from it.
You will get almost the same product from beech wood. It is plastic, which is important when processing products. Beech elements can be easily bent. The blanks are impregnated with various compounds, this increases their service life. Finished balusters are varnished.
Among the disadvantages of beech, it is worth noting that it is deformed during the drying process. Beech is great for imitating mahogany and walnut products.
Ash wood can be used to make racks. Outwardly, this tree is similar to oak, but is considered less durable and hard. The wood is quite elastic and dense. Ash does not rot, which significantly extends the service life of products.
Birch. Balusters are made from it the least often, since this breed has average density characteristics. Wood tends to crack, and is also prone to rotting. However, birch is easy to glue, polish and paint.
Balusters can be made from larch. In finished form, they have a brown color or shade. This breed is less durable than oak. However, over time, strength increases. Larch almost does not deform, but sometimes drying can cause internal cracks.
Wooden balusters are also made from pine. The material is easy to polish. Products are resistant to temperature changes. The disadvantage is that the paint penetrates the wood unevenly, and this leads to a decrease in the quality of the coating.
Production stages
Balusters are different forms. Because of this, do-it-yourself baluster making techniques differ, have features. For example, flat balusters are made from polished boards, or bars are used in work.
Carefully cut the board. Using the template, transfer the outline to each blank. Then cut out the elements. To get the job done faster, use a jigsaw.
You can collect several cuts of the board, securely fix them in place. Draw a contour on the upper cut, cut out the blanks. So you will receive several products at once. Finish the cuts and sand with sandpaper.
Another way to manufacture products with your own hands is to work with a solid bar. After it has been given a general shape, you can cut it into several elements. Next, the blanks need to be processed. The device of a ladder from such elements will not be very difficult.
For the production of square posts, first buy a bar of the required section, then saw it into blanks of the desired height. The balusters will be processed by hand. As for round products, bars are needed for their production.
Using a baluster making machine will speed up the work.
Video about the manufacture of wooden balusters:
Conclusion
The easiest way to make flat balusters. This does not require special skills, and only a jigsaw is needed from the tools. If you need carved elements or balusters made of precious wood, then it is best to contact specialists for their manufacture.
Balusters, or curly posts for railings and fences, are made of various materials: concrete, stone, metal, plaster. Consider the types and cost of wooden balusters. The most popular are turned wooden balusters, presented on the Russian market in a large assortment. The fact is that a tree, with the help of a lathe, can be given any shape.
Our business valuation:
Starting investments - from 150,000 rubles.
Market saturation is average.
The complexity of starting a business is 5/10.
There are the following types of balusters:
- volumetric square;
- flat: carved or smooth;
- spiral (hollow and full);
- conical;
- country (in the form of intertwined branches).
The price of wooden balusters depends on many factors, the main ones are: wood species, size, design complexity. The posts made by the master can turn any fence or railing into a real work of art. The wood is easy to work with. With the help of simple equipment, the baluster can be given any shape: a flower, a fairy-tale character, and so on. But the more complex the carving, the more expensive the cost of the baluster. Beautiful wooden staircase, a porch or a fence will cost those who wish a round sum. Therefore, many people are faced with the question of which is better: to buy wooden balusters or to make them yourself.
Making wooden balusters with your own hands is not only the most cheap way decorate your home. The production of columns and posts for railings and fences can be considered as a home business that does not require large financial investments, but brings a stable profit.
Product description and manufacturing scheme
Taking up the manufacture of wooden balusters, you need to familiarize yourself with their structural features including:
- base, fixed on the floor, threshold, steps with the help of a balustrade (rail);
- decorated central part;
- support for railings or handrails.
A simple instruction on how to make a baluster in a small production workshop is as follows:
- The choice of material for supports depends on several factors: the material of the main structure, the requirements for the appearance of the product and the method of fastening.
- Determination of the size of the balusters. It should be remembered that when installing the supports, their height goes a little. Therefore, for a railing with a height of 90 cm, the best option there will be columns whose length is 85 cm.
- Plain edged board disintegrated into square blanks of the same size. Machine equipped circular saws, handles such elements quickly and easily.
- Calibration will help to give the product an even and smooth appearance.
- The workpiece is cut on a cross-cutting machine: damaged areas, chips and other defects are removed.
- With the help of a lathe, the center of the product, the base and the support are formed.
- Once the baluster has received the desired shape, you can proceed to decorative works: carving, applying paint, varnish or impregnation.
Workshops, whose activity is the manufacture and sale of wooden balusters for stairs, often accept turnkey orders. That is, the specialist performs a full cycle of work, from measurements to installation. In this case, the shape of the baluster is developed jointly with the customer and executed according to the approved sketch.
The choice of wood for the production of supports
In the manufacture wooden poles most often used ash, pine, oak, larch.
The choice of material is based on the following factors:
- hardness;
- durability;
- wear resistance;
- fiber structure;
- color;
- price.
If it is planned to install wooden balusters in structures installed on the street, then the main parameter when choosing should be moisture resistance and resistance to decay.
The main advantage of pine is the low cost and softness of the wood, which makes it easy to process. Pine supports wear out quickly, are afraid of water and cannot bear heavy loads.
The price of ash balusters is higher than the cost of pine poles. But such columns will last much longer. At the same time, ash is able to withstand high mechanical loads. Hammering nails into such material, as in all hardwoods, should be done carefully, preventing cracking of the board.
Larch, like oak, has an optimal price-quality ratio. The red-brown material is endowed with high wear resistance and durability, and is also not affected by moisture and decay.
Handrail post production equipment
Circular milling machine with CNC OR-1500
The workshops use various woodworking machines to produce balusters.
For example:
- balusters with a round section are made using a lathe;
- manually or using special machines, the thread is applied to square or rectangular supports;
- to make flat wooden balusters with your own hands, you need a milling machine.
The choice of equipment depends on the type of finished product, the complexity of manufacturing and the expected production capacity. What matters is technical specifications machine, providing speed and high quality of work. A lathe can be purchased at a price of 8,000 rubles.
But to make carved wooden balusters to order is possible only with the help of a special milling machine with CNC, provided with a special program capable of performing a drawing on a tree of any level of complexity. The cost of such a unit is about 100,000 rubles.
You may also need a variety of milling and turning cutters, grinding fixtures and copiers.
Do-it-yourself home production of wooden balusters does not need complex installations. The master needs only a lathe, chisels, a metal round rod (sting), sharpening and paintwork materials.
Installation of balusters
Installing wooden balusters is not a difficult task. It is important to observe a certain distance between the mounted supports and control the reliability of fixing each element.
Security and rigidity wooden structure provide balusters installed every 15 cm.
The installation algorithm is simple:
- measurements are taken and the places for installing the columns are determined;
- the place for fasteners are balusters fixed on the basis of the structure;
- holes are drilled under the fasteners in the steps and columns;
- the fastener (dowel), as well as the railing, is fixed with glue;
- installation is completed with the installation of handrails.
Fasteners for supports are special rods with a diameter of not more than ¼ of the diameter of the baluster, and the length is equal to 2 diameters.